Poly Bag Packaging supplies
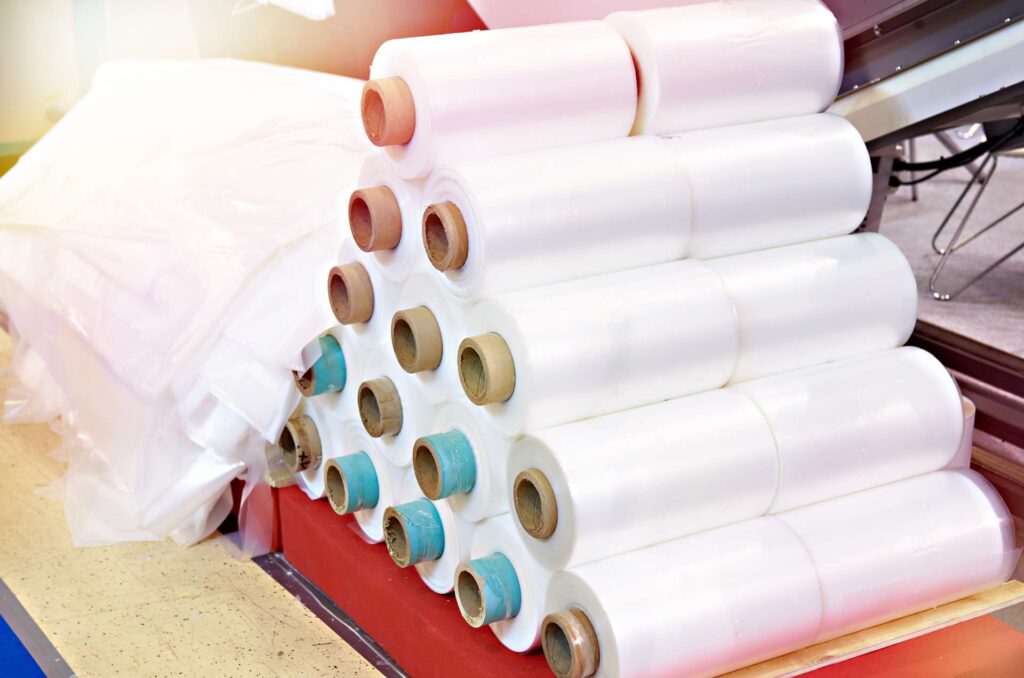
Poly bags play a crucial role in product packaging as they provide a cost-effective, durable and versatile solution for protecting and transporting various goods. These bags are made of polyethylene, a lightweight and flexible material that offers excellent protection against moisture, dust, and other environmental factors. They can be easily customized in terms of size, thickness, and color to meet the specific needs of different products. Additionally, poly bags are eco-friendly as they are recyclable and biodegradable, making them a responsible choice for companies looking to reduce their environmental footprint.
Poly Bag Options
- Custom size bags & printed bag
- Stock Size bags
- Shopping Bags
- Ziplock Bags
- High Density Bags
- Pallets Shrouds
- Bags Heat Sealer
Ready to upgrade your packaging strategy? Let's do it together!
Fill out the form below and we will be in contact.
Poly Bag FAQs
A poly bag, short for polyethylene bag, is a versatile packaging solution made from flexible, durable plastic. These bags are widely used across various industries for packaging products such as food items, apparel, and industrial components, offering protection against moisture, dust, and other environmental factors.
Sealing methods for poly bags vary based on the bag type and intended use:
- Heat Sealing: Commonly used for flat poly bags, this method employs heat to fuse the bag’s open end, creating an airtight seal.
- Adhesive Closures: Some poly bags feature a built-in adhesive strip that allows for easy sealing by folding the flap over the bag’s opening.
- Zipper Closures: Resealable poly bags come with integrated zipper tracks, enabling multiple openings and closings.
- Tape Closures: Applying adhesive tape over the bag’s opening is a straightforward method suitable for various bag types.
The choice of sealing technique depends on factors such as the bag’s material, thickness, and the level of protection required for the contents.
Printing on poly bags enhances branding and product information display. Two primary printing methods are:
- Digital Printing: Ideal for short runs and designs requiring multiple colors or intricate details. This method offers quick turnaround times without the need for physical printing plates.
- Flexographic Printing: Suitable for larger production runs, this technique uses custom-made plates to transfer ink onto the bag. While it involves initial setup costs for tooling, it becomes cost-effective at higher volumes.
Selecting the appropriate printing method depends on factors like order size, design complexity, and budget considerations.
Traditional poly bags are made from petroleum-based plastics, raising environmental concerns due to their non-biodegradable nature. However, advancements in materials have led to more sustainable options:
- Recycled Content: Some poly bags are manufactured using recycled plastics, reducing reliance on virgin materials and minimizing environmental impact.
- Biodegradable Alternatives: Innovations have introduced biodegradable poly bags that break down more readily in the environment.
Choosing eco-friendly poly bags contributes to sustainability efforts and aligns with environmentally conscious practices.
Traditional poly bags are not biodegradable and can persist in the environment for extended periods. However, biodegradable poly bags are available, designed to decompose more rapidly under specific environmental conditions, thereby reducing their ecological footprint.
Yes, many poly mailer bags are recyclable, especially those made from polyethylene. It’s essential to check local recycling guidelines, as some facilities accept these materials through designated drop-off programs. Ensuring that poly mailers are clean and free from labels can facilitate the recycling process.
The weight of a poly bag varies based on its size, thickness, and material composition. For instance, a standard 10” x 12” poly bag with a thickness of 2 mils typically weighs around 0.5 ounces. Accurate weight measurements are crucial for shipping calculations and cost assessments.
Proper measurement of poly bags ensures they accommodate the intended contents and comply with shipping requirements:
- Width (W): Measure the bag from side to side.
- Length (L): Measure from the bottom of the bag to the opening.
- Gusset (G): For gusseted bags, measure the depth of the side folds.
The formula for determining the bag size is:
For flat bags: Width (W) x Length (L)
For gusseted bags: Width (W) + Gusset (G) x Length (L)
Accurate measurements ensure the bag fits the product properly and meets shipping standards.
Yes, poly bags can be fully customized to meet your branding and functional requirements. Options include tailoring the size, thickness, color, and printing. Whether you need vibrant, branded designs or specific dimensions for unique products, we can create poly bags that align perfectly with your needs.
Poly bags used for food or medical products must comply with strict safety standards and regulations. Our team ensures that all materials meet FDA and other relevant guidelines, providing safe and reliable packaging for your specialized needs. Always specify your product’s requirements so we can guide you to the right solution.